60 Tons/hr
e have developed a distribution center here with an integrated washing and packaging line for sixty tons per hour. After the line, we designed a distribution system. The distribution center can optionally be equipped with gravity roller sets. The project is for a large trader, who processes the potatoes from his own cultivation and from suppliers. There is only storage capacity for a few production days of packaged potatoes. Supplied potatoes cannot be stored, Therefore potatoes must be brought directly from the truck into the line. In this case, we speak of a docking station. The potatoes are delivered in potato trucks. The customer did not have a detailed logistics plan. The storage and shipping of the crops and packaged potatoes was not well organized. That is why we have developed a total plan to visualize the entire production with shipment. In line, we carry out measurements at critical points to keep an eye on efficiency. The efficiency applies to both the truck load, amount of soil and organic waste per ton. How many stones and clods. Quality control per truck. How many people do we need to be able to carry out the manual inspection properly? What is the grading scheme of the delivered potatoes? So we assess each truck whether it has met the contract or the expectations. The way of sorting and grading is mechanical. The reason for this is that the potatoes are supplied fresh. The line works about four months a year.
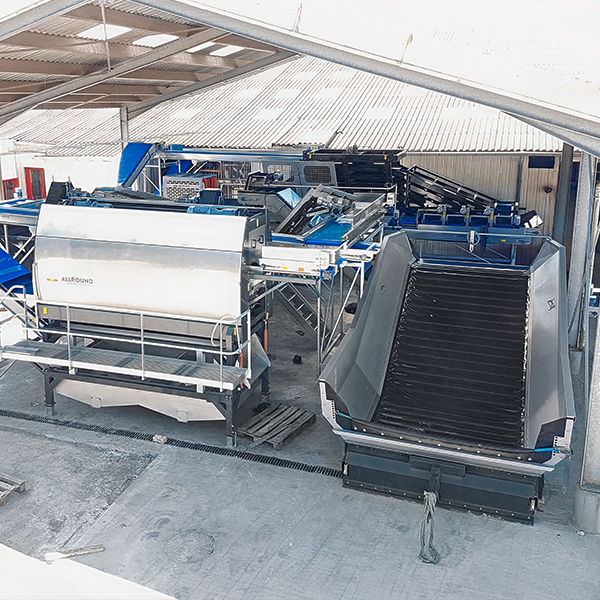
Zone 1 : Receiving and washing
The potatoes arrive in potato belt trucks. The trucks first have to cross the weighbridge. Here, in addition to the gross weight, the load factor that has been agreed is immediately recorded. For example, at least 27 tons. Under loading is charged to prevent unnecessary truck movements. At the reception there is room for two trucks, the second can be ready while the first is still unloading. The reception at the line is in a receiving hopper. The hopper has a large content and capacity but does not have an exceptionally heavy construction because the supply is with potato trucks. The price of this bunker is therefore favourable. After the receiving hopper the potatoes go to a destoner then to a skin separator. Here, old corn cobs and organic residues are removed. After destoning and skin separation, the potatoes come into a drum washer. After the washer, you can choose a polisher or a horizontal brushing machine. The choice depends on the type of potatoes, degree of contamination and skin quality. The washing part (Wet part) is separated from the sorting, grading and packing process. Water management is supported by a smart water recirculation system from Taneco. The Taneco purification system is very easy to install. The whole system is installed in a twenty foot container. We take care of the entire water management with drawings and calculations.
Zone 2 : Inspection and mechanical grading
The potatoes arrive in potato belt trucks. The trucks first have to cross the weighbridge. Here, in addition to the gross weight, the load factor that has been agreed is immediately recorded. For example, at least 27 tons. Under loading is charged to prevent unnecessary truck movements. At the reception there is room for two trucks, the second can be ready while the first is still unloading. The reception at the line is in a receiving hopper. The hopper has a large content and capacity but does not have an exceptionally heavy construction because the supply is with potato trucks. The price of this bunker is therefore favourable. After the receiving hopper the potatoes go to a destoner then to a skin separator. Here, old corn cobs and organic residues are removed. After destoning and skin separation, the potatoes come into a drum washer. After the washer, you can choose a polisher or a horizontal brushing machine. The choice depends on the type of potatoes, degree of contamination and skin quality. The washing part (Wet part) is separated from the sorting, grading and packing process. Water management is supported by a smart water recirculation system from Taneco. The Taneco purification system is very easy to install. The whole system is installed in a twenty foot container. We take care of the entire water management with drawings and calculations.
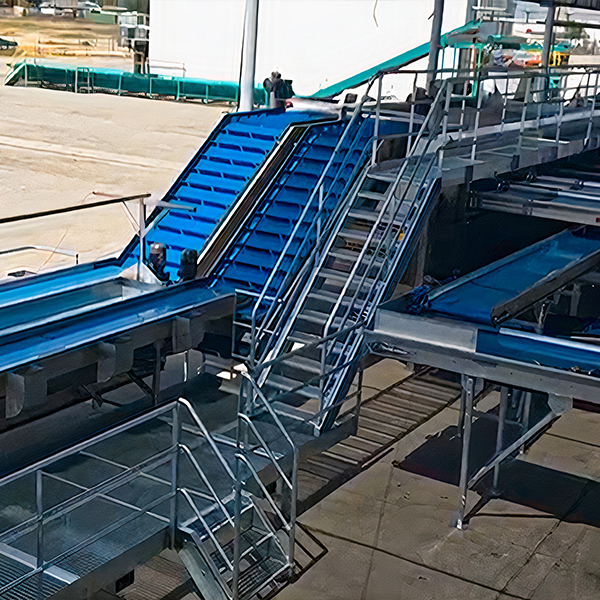
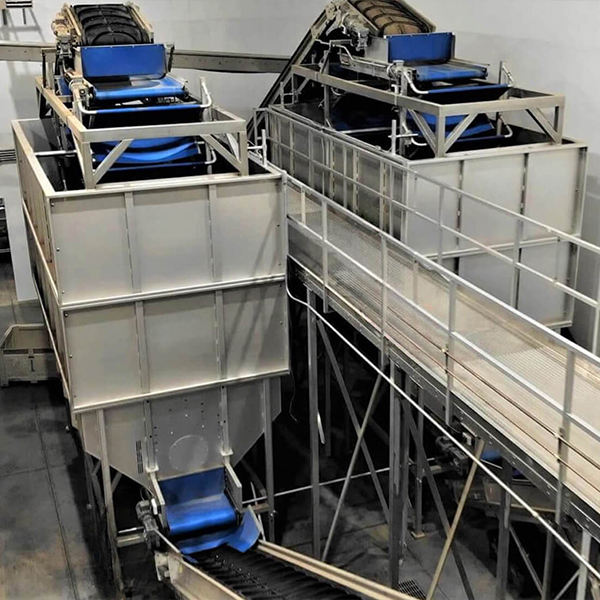
Zone 3 : Buffering
In zone three, the weighing, packing and palletizing area is integrated with the distribution system. From any storage hopper you can go to any weighing and packaging machine. We have made the distribution with the transport belts around the bunker block in such a way that you can easily select the grade and weighing and packaging machine on the tablet or central computer. For the weighing and packaging of, for example, undersize, a simple bagging machine is used. Here, bags of 50 pounds are made. Palletization is done manually using a pallet shaper. In the line is a box filler / jumbo bag included. For the two main sizes, two Upmann weighing and packaging stations have been proposed. An IPLA palletizing machine has been installed at one of the packaging stations. The IPLA palletizer is special for the cartons and RPCs.
Zone 4 : Weighing and packing
The distribution center is a logical system where the principle of first in first out is strictly applied. The production and shipping departments receive the orders from the sales department. The prepared orders are placed in a fixed system in the distribution center by the members of the production team. With the help of tablets, the orders and places in the distribution center are communicated to the employees of production. To support this, large electronic order screens are set up at the production location in the line. The same process takes place at dispatch. The employees receive the orders for dispatch on tablets. Large electronic screens are also set up at the dispatch department. Management by walking is a thing of the past. It is now a tightly organized logistics process.
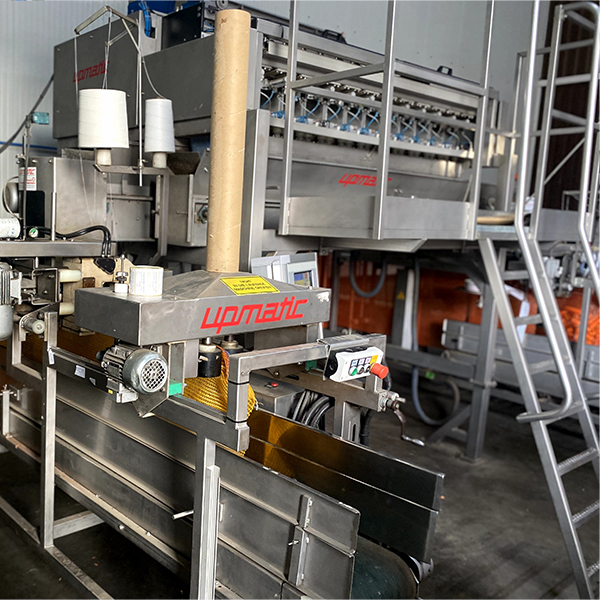