25 Tons/hr
For the displayed processing plant is a washingline. The washingline is not included in this project description. The installation is with a Hagen sorting machine with 16 outputs, one of which is returned. We have designed an installation in which we have adhered to our principle that once the potatoes are removed from the sorting machine, they are guided directly into the weighing and packaging machines without human intervention. The number of forklift movements compared to competing proposals was therefore very large. Another starting point was to keep the footprint as small as possible and the routing as logical as possible. We worked with ten storage/ even flow hoppers in combination with four single box fillers/ jumbo bag fillers. All storage hoppers are equipped with vertical filling belts to keep the drop height to a minimum. The entire installation is largely carried out in Stainless Steel. For a good overview of the storage hoppers, there are platforms around the hoppers. The entire installation is centrally controlled. The control is by means of a central computer and tablets. The installation has resulted in major labor savings. The control and line management has become very simple. The cooperation with the various suppliers in the Partnership of companies was particularly pleasant. We worked out more than fourteen options for the customer before we came to this final lay out
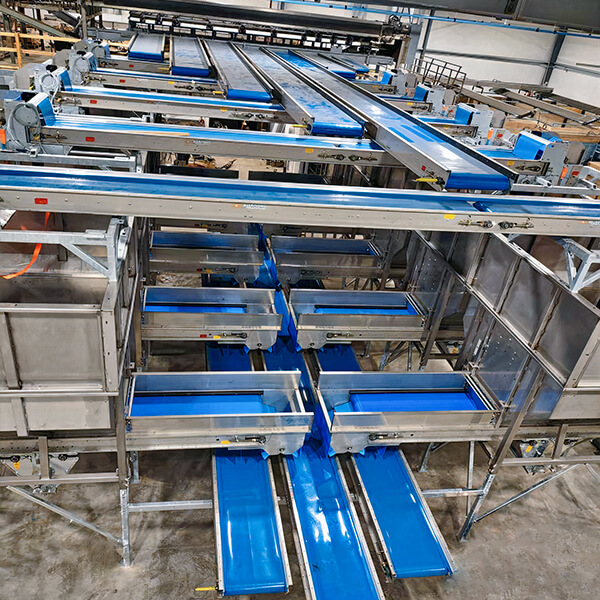
Zone 1 : Grading & Buffering
Existing Hagen sorting machine with sixteen exits of which a return for unsorted potatoes. These potatoes are once again brought over the sorting machine. From the sorting machine, the product is led to ten storage / even flow hoppers. The storage hoppers are all equipped with vertical filling belts. Output product from the bunkers is both left and right. From any bunker you can get to any packaging machine. The rejected potatoes are immediately removed and collected outside the processing area.
Zone 2 : Filling Macrons and Big bags
Four single boxes / big bag fillers are included in the bunker installation. Each hopper can be emptied in Jumbo bags or Macron / cubic boxes. To empty in jumbo bags or Macrons only happens when a specific size and quality has not been sold. A second possibility is that if you want to pack two grades with the same weighing and packaging unit. You will then temporarily store it. In practice, this will not cause much of a stir because there is a fairly large buffer time. The Macron / cubic boxes can be brought back into line with a storage tipping device. From here you can go to any weighing and packaging machine. Around the entire storage hopper installation there are transport belts. With the help of these belts you can go from any bunker to any weighing and packing station or single jumbo bag/ box filler. The outfeed belts of the storage hoppers are equipped with a distribution valve. The entire bunker installation in combination with the cleverly applied discharge belts is extremely flexible.
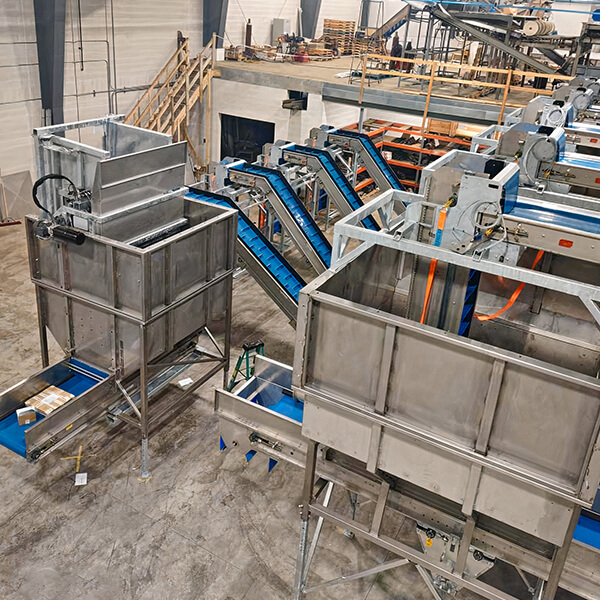
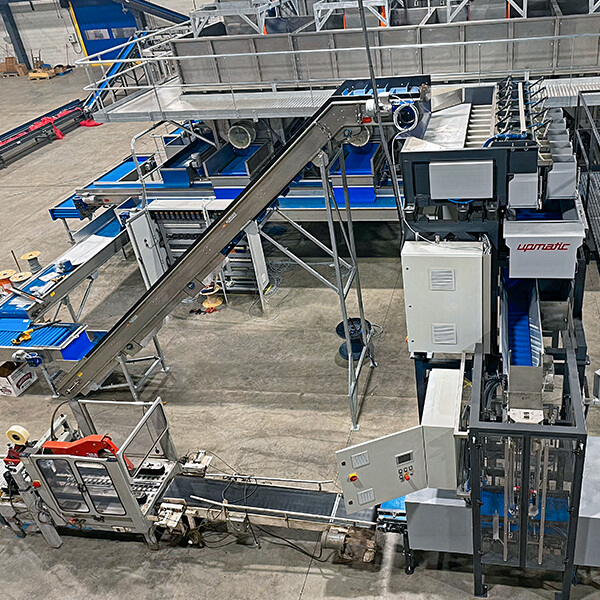
Zone 3 : Weighing and packing
Four weighing and packaging stations are directly connected from the storage hopper block. Three stations for net bags. One weighing and packaging station for cartons. Type 2711. big products. 11 cups. Capacity 50 pounds bags 17 per minute = 22 tons. Carton filler by lifting buffer type AST 22.5. After the packaging machines, there are two bailers. Here, small packages are packed in a master bag. The master bags can be returned to the robot arm for automatic collection in large cardboard boxes. Masterbags can also be guided to the round packing table for manual collection. For weighing and packaging of cartons is an Upmann installation. An automatic cardboard erector feeds the Upmann machine.
Zone 4 : Bag transport, counting, packing into sacks, outlet belt
The UPMATIC 1352UPA is a fully automatic baler for Raschel bags. The machine consists of the separating and counting device and the net bagger itself.The UPMATIC 1352UPA processes Raschel net from the roll which is separated, filled, and closed in the machine. It can process products such as clip nets, poly bags and Raschel sacks weighing 0.5-5 kg.Two complete lines were installed in the new Nuto plant. These receive the bags from several weighing machines, each with two Wicket bagger.The unit at Nuto was designed as a bailing line for two product lines. The bags coming from different wicket baggers are separated and distributed on to a buffer belt by a gate. When a batch is complete, all the bags belonging to the batch are transported to the bailer.After filling, this baler bag is sewn and separated in the 1352 UPA and then transported on to the fully automatic palletising system.The output of such a line depends on the products fed in and is between 90 ppm for 1 kg clipped net and 40 ppm for 5 kg Raschel net or film bags what means between 5 and 8 baler bags per minute.
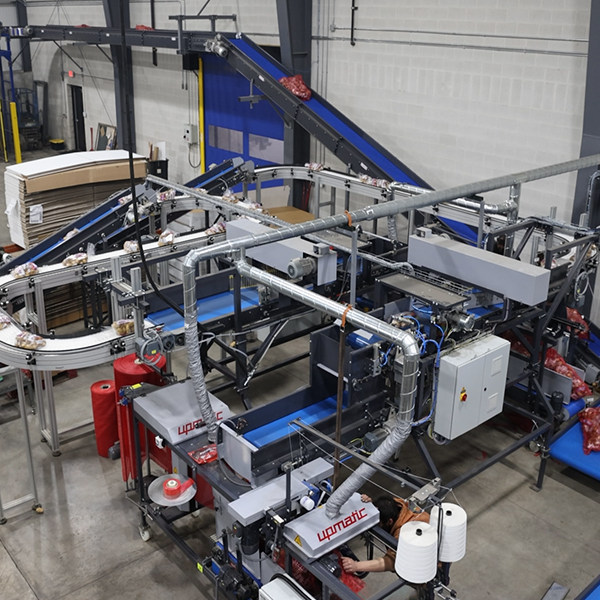