Onion 25 t/h shallots 7t/h.
For a customer in Western Europe we delivered a reception, onion topping, grading and optical sorting and weighing and packaging installation. The line is made for processing onions and shallots. So we have created an integrated line for the processing of shallots and onions. The capacity is about seven tons for shallots and fifteen tons per hour for onions. The onions and shallots are supplied from own storage or from suppliers both in cubic boxes. After the reception hoppers an electronic stone separator is placed. Two onion toppers for onion as well as for shallots. A radial grader with three sizes has been placed in front of the onion toppers to achieve the best possible result with as little damage as possible. The onions and shallots are pre-graded in three sizes. Two sizes for the two onion toppers with different sieves sizes and one size for oversize or undersize. Undersized or oversize can be collected in boxes or big bags or disposed of directly to the central waste system, The onions are optically sorted and graded whereas the shallots mechanically with a radial grader with four outlets. The whole is a green field project. The entire installation is placed in a limited space with a mezzanine. The mezzanine has the great advantage that enables to design a perfect logistics system.
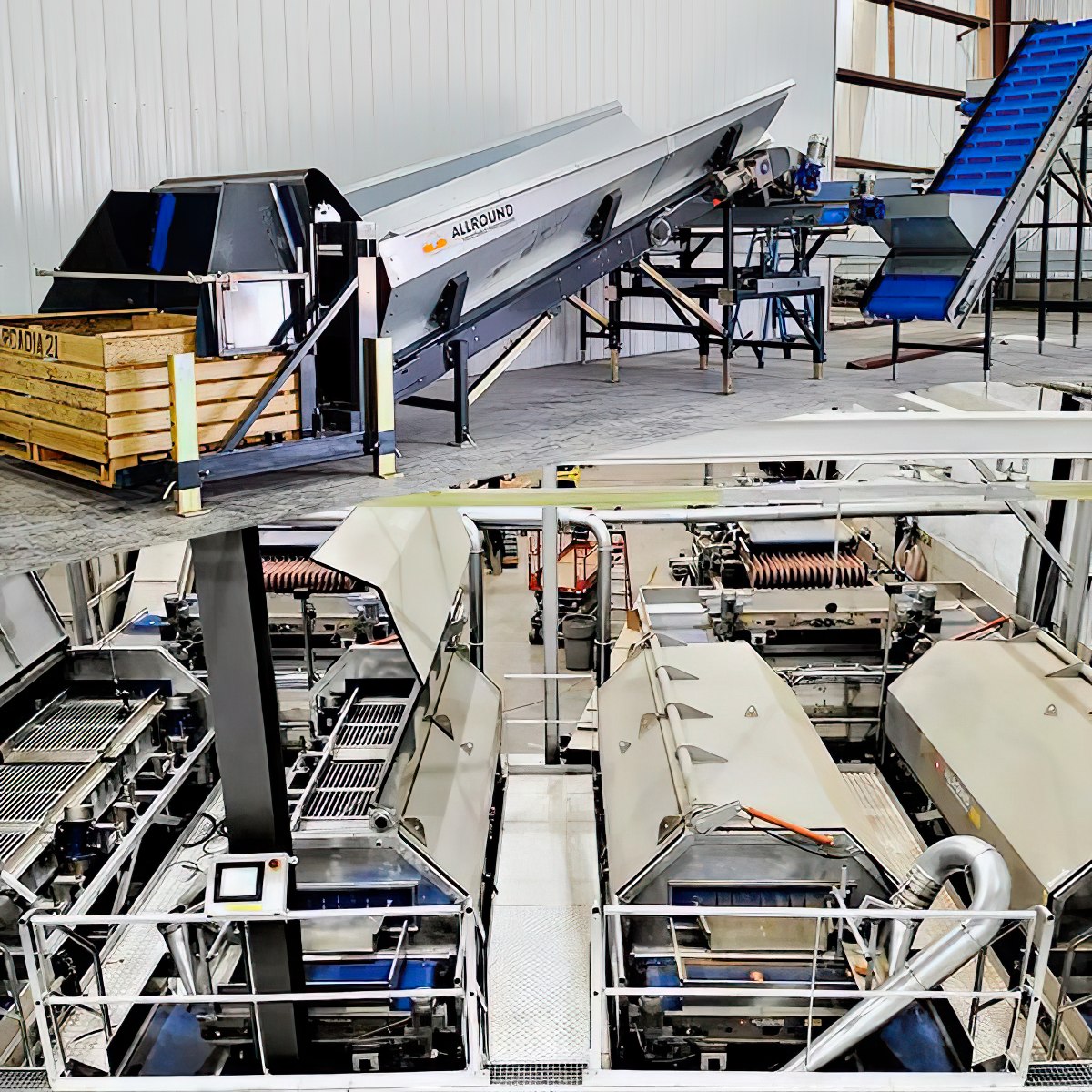
Zone 1 : Reception and processing.
The input of the onions and shallots in the line is with cubic boxes. The boxes are inserted into two reception hoppers with a tipper. After the two hoppers, the product is transported on a collection belt to a roller set .and then to an electronic detonator. Onions or shallots that are already fit to be packed can be transported directly from the reception hoppers to any weighing and packaging station. These onions or shallots are form suppliers or from storage. After the electronic destone, the onions go to the pre-grader for the onion toppers. There are two onion toppers with three blades. Blades can be changed with a special crane system. The radial pre-grader has three outputs. The undersize or possibly oversize can either go to the central waste belt or to a box / big bag filler. Onions from the onion toppers go directly to the mezzanine. All waste and dust released during this process is either extracted or collected on a central transport belt.
Zone 2 :Optical and mechanical sorting on the mezzanine.
The onions and shallots go to the mezzanine after being topped or via the by pass when they not needed to be topped. On the mezzanine, a choice can be made to feed to the radial grader or to the optical grader/sorter. In practice, as already indicated, the shallots are sorted over the radial grader and the onions over the optical grader / sorter. The shallots of the radial grader are collected in cubic boxes via vertical finger belts. With a full box, an acoustic and visual signal is given. There is enough buffer on the belt of the radial sorter to change the box. The onions are sorted internally and size on the optical grader/ sorter. The optical grader / sorter has eight sizes. Two extra outlets are available to accommodate any peak capacities. In front of the eoptical grader / sorter there is at least space for two people for manual inspection. The manual rejected onions and the rejected onion of the optical grader / sorter are collected on the central waste management system.
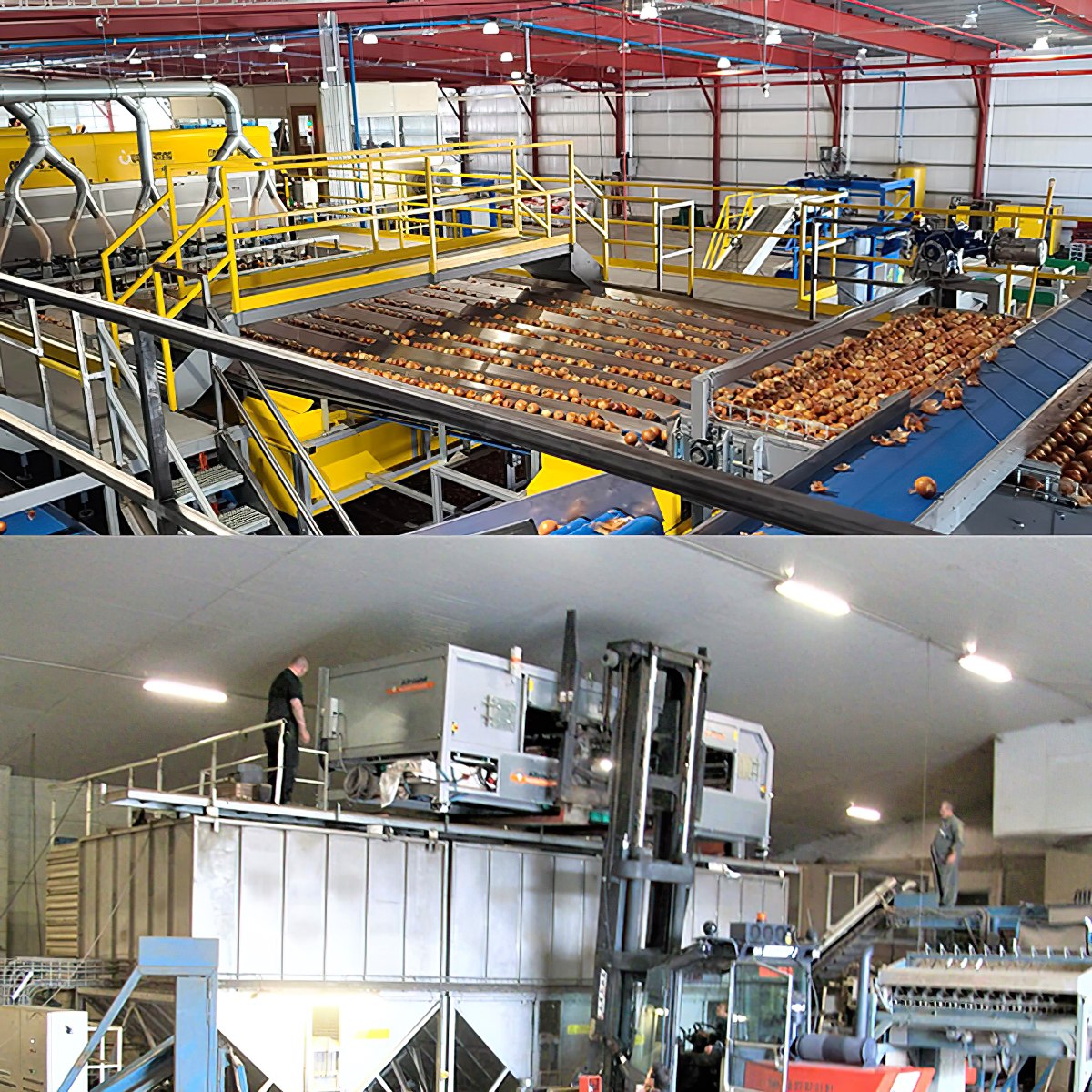
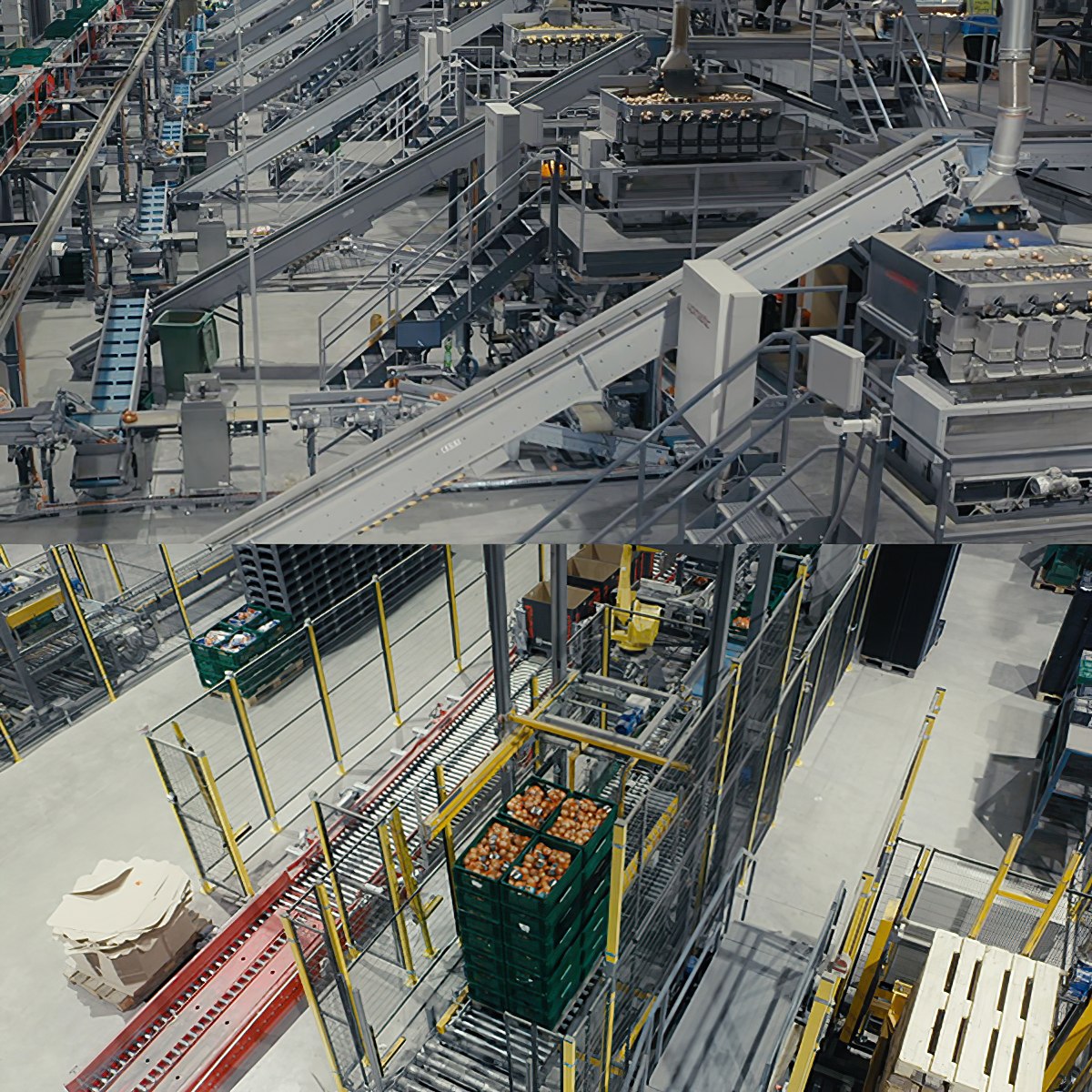
Zone 3 : Collection, distribution and weighing and packing
The graded and sorted onions from thee optical grader / sorter are collected in storage hoppers. The name of storage hoppers is not correct. These hoppers are evenflow hoppers for the weighing and packaging machines. The capacity of the weighing and packaging machines and the contents of the even flow hoppers will in the vast majority of cases be sufficient to ensure that the process runs smoothly. The whole line is designed that in most cases the onions go directly in the final packaging without intermediate collection in cubic boxes. For exceptional cases, there are two additional storage / evenflow hoppers to accommodate peak production. For example, you can think of a particularly big sized party where ninety percent has the maximum size. After the even flow hopers there is a sophisticated system of conveyor belts. From here you can go from any even flow of any size and quality to any weighing and packaging station. Also you can empty any storage / even flow hopper in a bi bag filler. For onion ready to pack you bring them in the line with one of the receiving hoppers. From here you can go to any weighing and packing station
Zone 4: Central waste management, dust extraction and weighing and packaging machines.
A central waste management system is integrated into the line / installation. The solid organic waste and the rejected onion both those of manual and optical grader / sorter are collected on a central belt. This belt dissolves in the central waste collection cabin where the dust from the dust extraction is also collected. The dust extraction system sucks off the dust and skins at any point of the line where the onions or shallots move from one belt to another or entering any machine. In this way we create a clean working environment in which an added value is also given to the product. On the weighing machines and, if necessary, on the packaging machines, the dust and loose skins are also extracted. This way you get a particularly well looking and presentable product in the packaging.
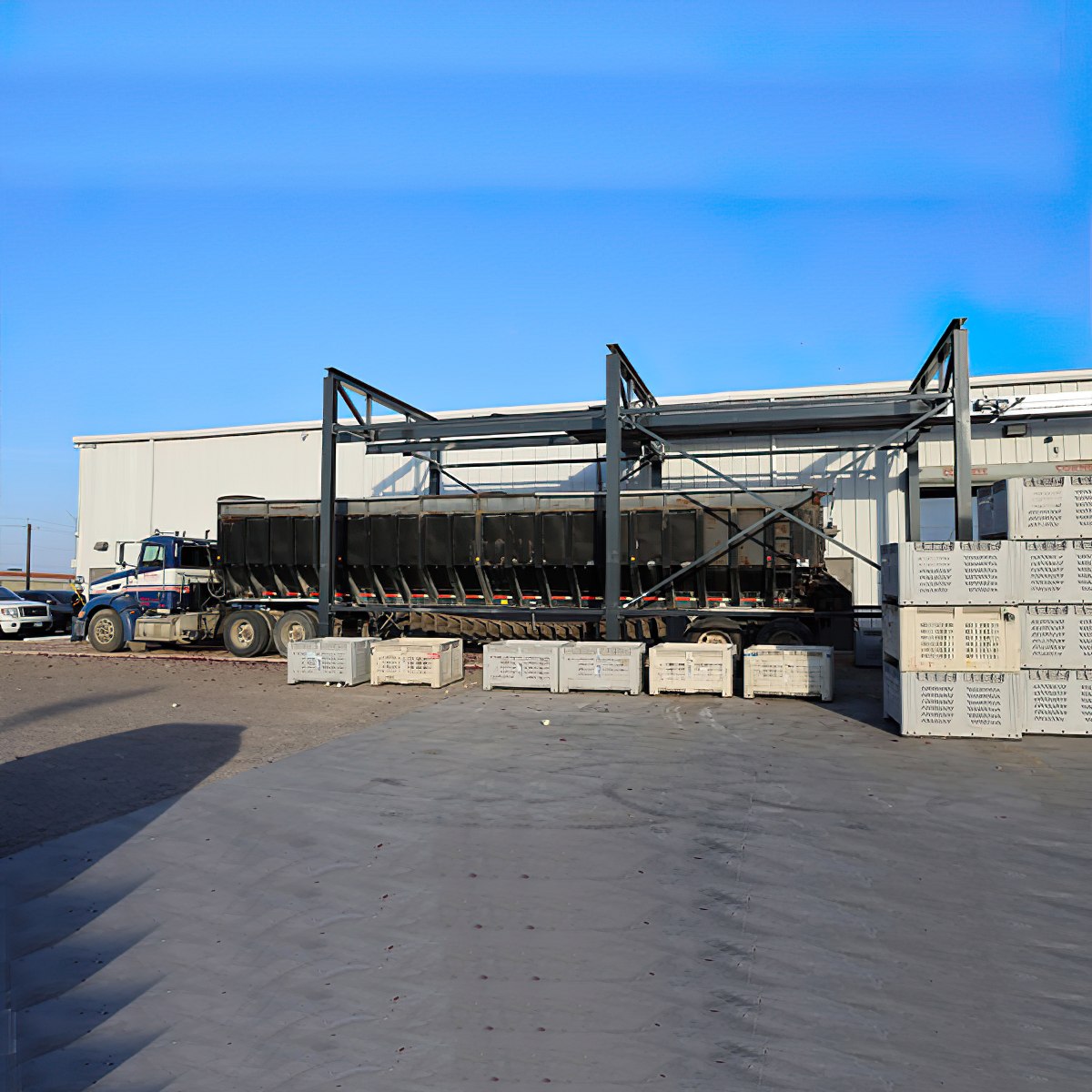