10 – 15 tons/hr
For a customer who grows potatoes and onions organically, we have created this integrated processing line. The company grows both potatoes and onions. You also can brush and grade red beet on this line. The potatoes and onions are grown in different varieties. The onions and potatoes differ in shape from round to elongated. We wanted a solution where both the products could go over the radial grader and over the shake grader. This separate process of the radial grader and that of the shake grader had to be integrated with the rest of the line. After all, two separate lines would be much more expensive and have a much larger footprint. The line is extremely suitable for the growers and those wholesalers who must be able to offer a total package to their customers. The line is quite easy to extend with a washing machine. The line is divided into a dirty department and a clean department. At the dirty department, the products are received from both directly from field, from the storage and suppliers. In the clean department, the products are selected manually and mechanically graded and weighed and packed. In the dirty department, the product is brought into the line at the receiving hopper. This can release a lot of dust. In the dirty department, the potatoes are brushed and the onions are topped at. With a simple industrial curtain, the dirty and clean departments can be separated. This separation benefits the product and the working conditions.
For the weighing and packaging department, we have opted for a stand-alone solution. The Upmann weighing and packaging combination is fed with a Storage Hopper Box tipper. All grades can be packaged as desired. This solution is very efficient and interesting from a budgetary point of view.
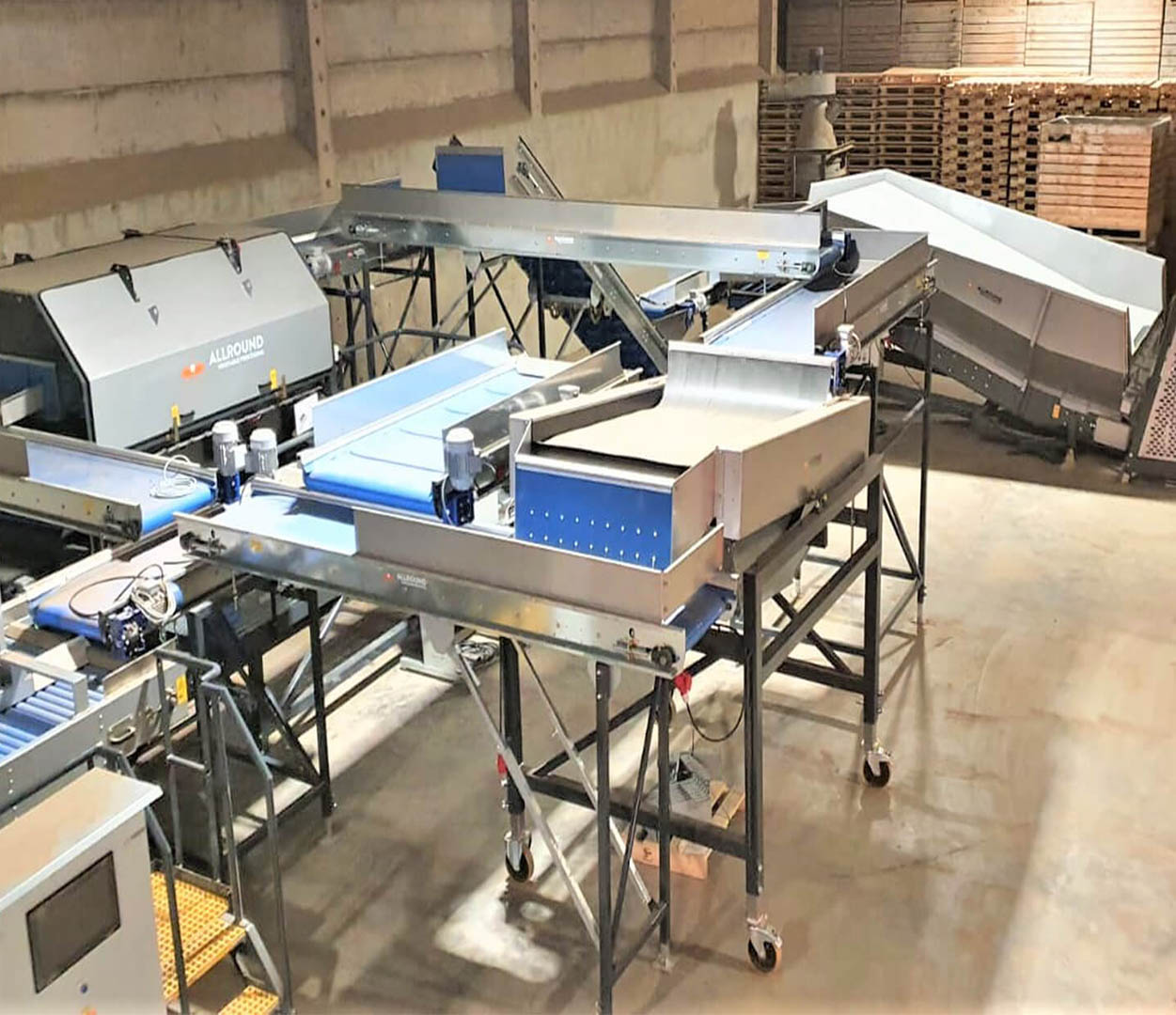
Zone 1 : Receiving, brushing and topping
In zone 1, the product is brought into the line. The potatoes and onions can be freshly harvested or from the cold store. The products are from own cultivation or from suppliers. The reception hopper is suitable for cubic boxes, big bags, smaller tip trailers and Bottom potato belt trucks. A spiral roller set has been installed at the receiving hopper. Here, many loose onion peels are separated and disposed of. When processing potatoes, you already lose a lot of loose soil here. The peels and loose soil are fed out with a transport belt. After the reception hopper there is the choice to go to the onion peeler or to the potato brush machine or directly to the inspection table. The onion topper is a three knife version. The capacity of the onion topper, depending on the size of the onions, is between ten and fifteen tons per hour. When the product enters at the receiving hopper, a lot of dust and peels are spread. We can offer you a tent with dust extraction to prevent this. With the onion topper, there is the possibility to mount dust extraction at infeed and on the of the waste belt. With the potato brushing machine there is also the possibility to make a tent on the brushing bed with extraction. With this relatively small investment, you keep the processing room nice and clean. Meconaf has a great deal of experience in such installations. At the brushing machine there is a bypass. With the bypass you can bring the potatoes and onions via the inspection unit to one of the sorting machines without processing.
Zone 2 : Manual inspection
The onions and potatoes and possibly red beet are collected after the onion topper, potato brushing machine or bypass and brought to the roller inspection table. The main products are onions and potatoes. The cultivation takes place quite northerly therefore the skin of the onions is thick. The advantage of the roller inspection table is that the product rotates and can therefore be seen from every side. At the beginning of the roller inspection table, it is advisable to apply an extraction point for dust. Another option is to build a cabin around the reading table with over preasure. In the middle of the roller inspection table an aisle is made. The aisle is for the rejected products. The aisle dissolves on a discharge belt. The good product goes from the roller inspection table in an elevator tot radial grader. The elevator has a swanneck for a minimum drop height on the infeed belt of the radial grader.
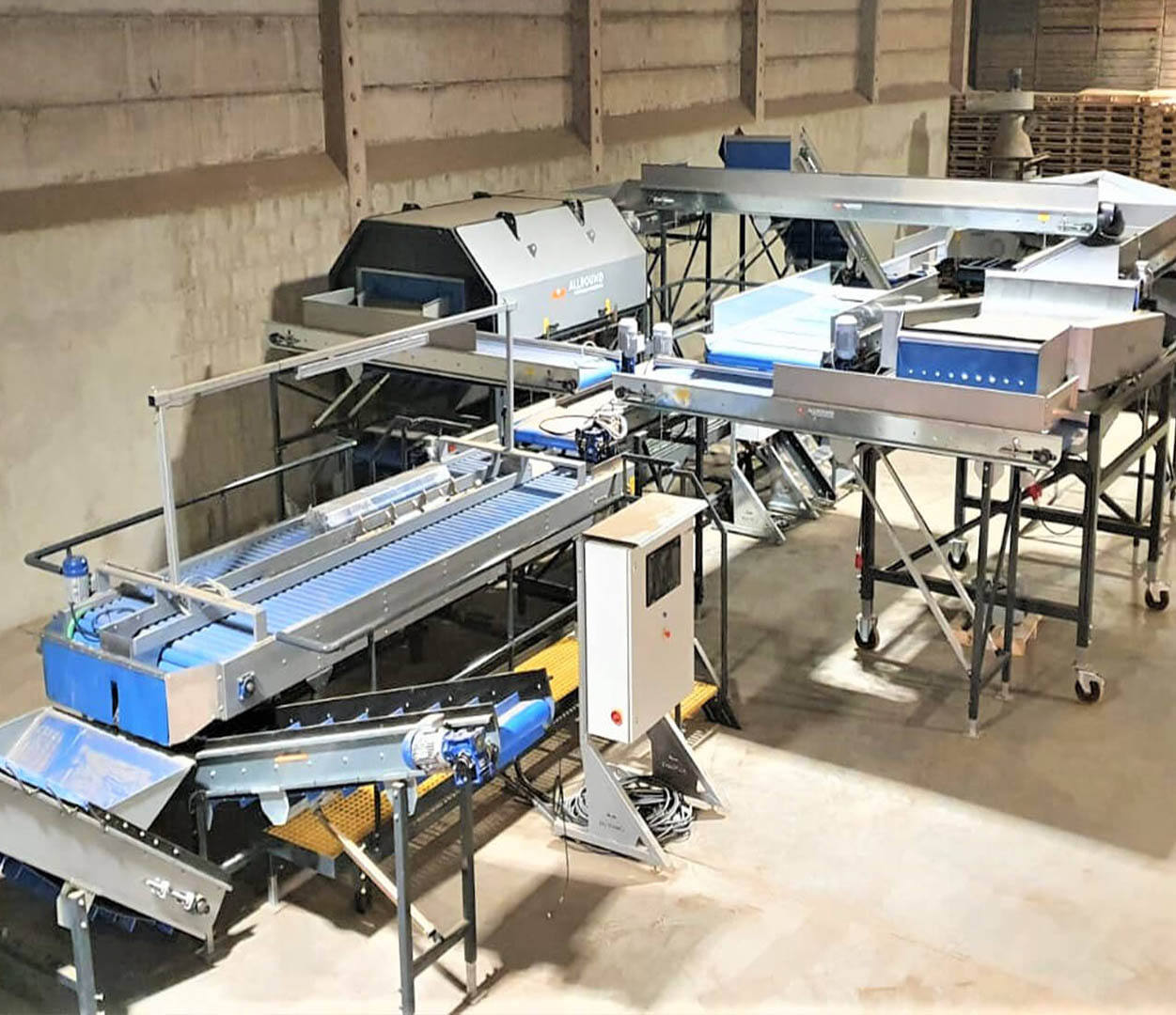

Zone 3 : Shake and radial grading
In zone three, we have integrated two ways of grading with each other. We put a radial grader and a shake grader against each other. After the manual inspection table you have the choice of the radial grader or the shake grader. The elevator dissolves on the feed belt to the radial grader. This band is reversible. Forward to the radial grader to the rear to the shake grader. At the line is a box filler annex big bag filler. Every size of both the radial grader and that of the shake grader can be guided to the box filler / big bag filler. All other grades are collected in cubic boxes. The line has a small footprint and is maximally flexible. An ideal setup for a whole sale dealer who has to deliver multiple products and who has to be able to deliver both sqaire size, shake grader, and bars size, radial grader. We have already delivered many such lines / installations. For all specific requirements and for every available space we know how to come up with a nice suitable solution together with you. We have many examples for inspiration in our database. We are happy to show you these during a video conference.
Zone 4:
Lorem ipsum dolor sit amet, consectetur adipiscing elit, sed do eiusmod tempor incididunt ut labore et dolore magna aliqua. Ut enim ad minim veniam, quis nostrud exercitation ullamco laboris nisi ut aliquip ex ea commodo consequat. Duis aute irure dolor in reprehenderit in voluptate velit esse cillum dolore eu fugiat nulla pariatur. Excepteur sint occaecat cupidatat non proident, sunt in culpa qui officia deserunt mollit anim id est laborum.
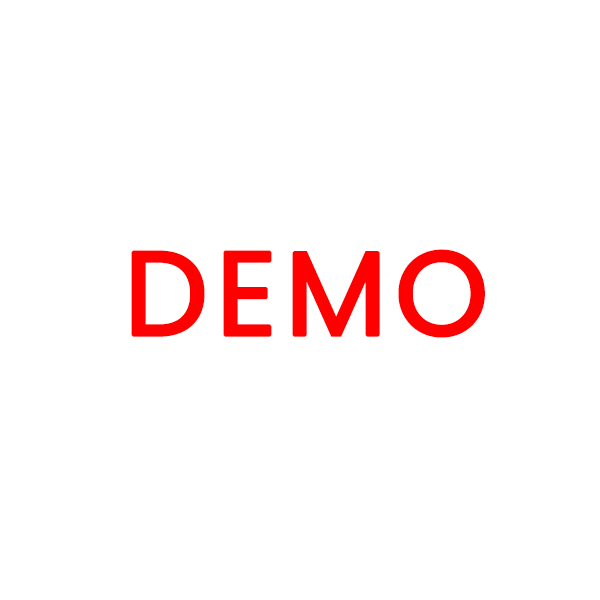