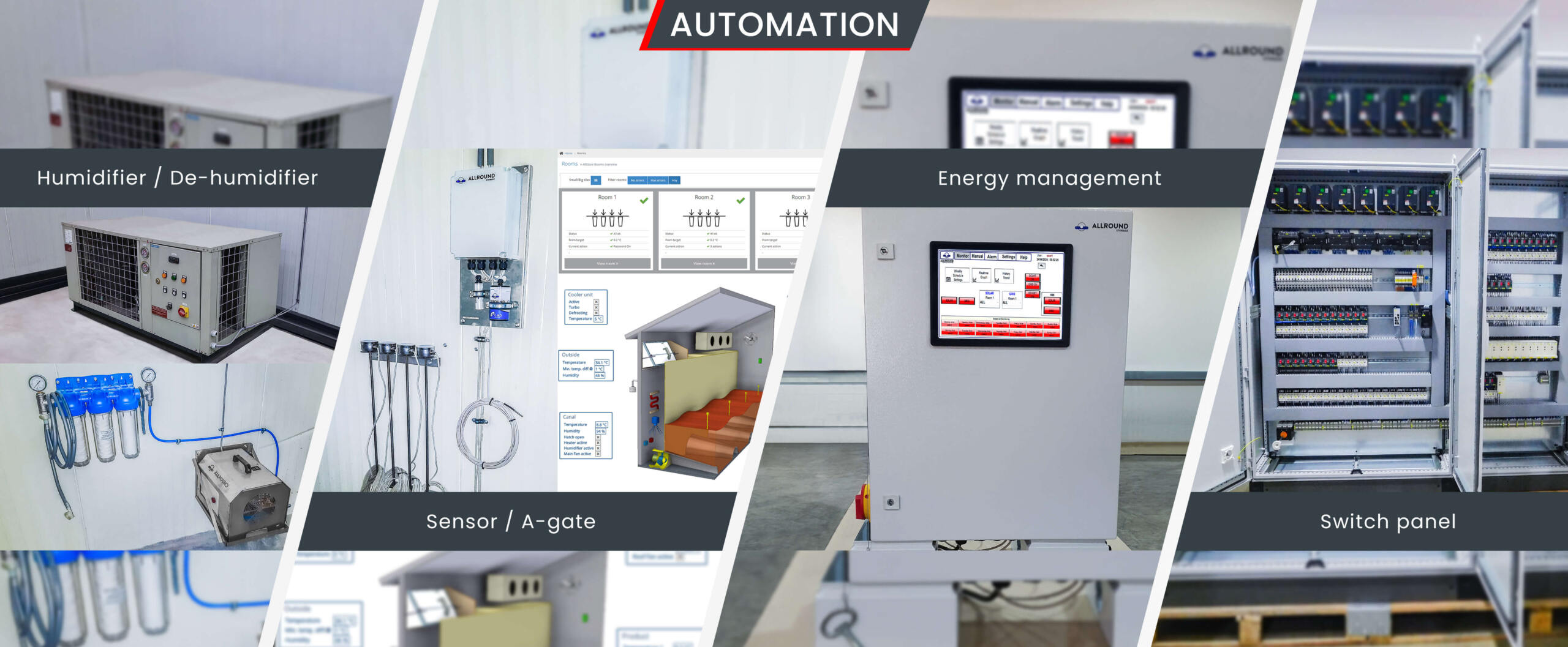
Automation and Its Parts
Allround produces most of the components for a cold store for agricultural products in-house. This keeps the supply lines and delivery times short. By keeping everything in-house, we can maintain a competitive price level. However, we do work closely with other companies to assess whether the latest trends are of interest to our clients. The latest development for us: the Allround Energy management system. We have developed our own software that calculates when the Allround Turn Key Coolers should be activated. The Energy Management system also determines the most advantageous energy source. The different energy sources are grid, generator and solar energy. An extensive manual made by a professional wrtier is part of the standard repertoire at Allround Storage. Our automation team works every day to optimize processes and operation. We have an extensive staff for electrical panel construction and installation. We only use the best brands here.
Components :
Tailor. Cable: LAPP.
PLC’s: Omron
HMI screens: EXOR
Panels: Rial optional in Stainles Steel
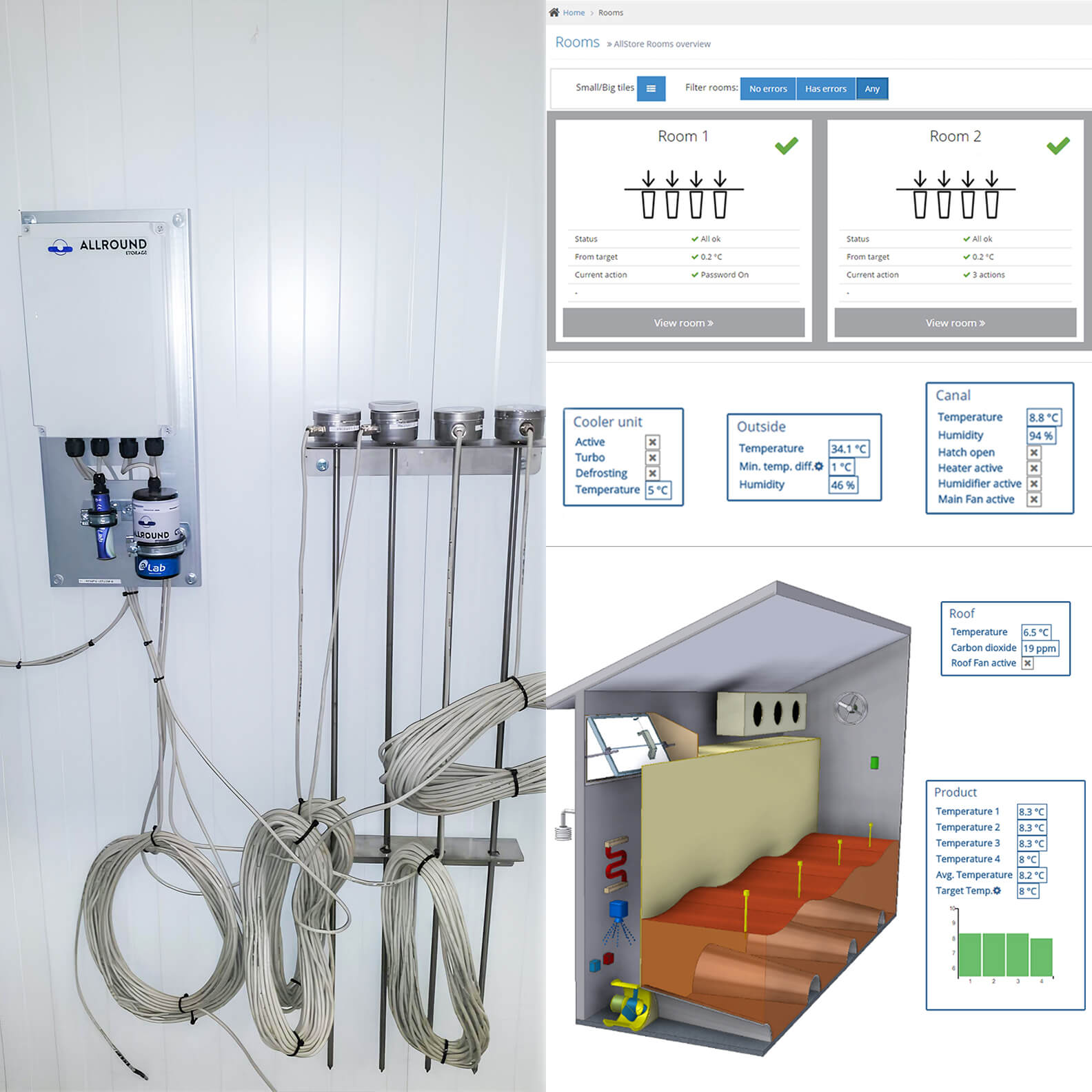
Sensor & AGATE- 1
If you, as an operator, keep a close eye on these values, you can’t really go wrong. The measurements are all recorded electronically. The contractor (e.g. a French fries factory) can also retrieve and analyse these values online via the system if desired. This analysis can be retrieved per day, per week, month or for the entire retention period. This data (storage data) can also be imported directly into the ERP system of the contractor (e.g. French fries factory).
It is essential to keep the system on constantly. This is also better for installation such as the sensors, storage computer and the All store. Moisture effects are thus largely avoided by low heat generation. This outweighs a minimal cost due to additional energy consumption. The whole system, the incredible usability and ease of use, is provided as standard as mentioned earlier.
Sensor & AGATE – 2
A gate communicates with the various storage computers and stores data. This data is displayed via a central computer, via a Wi-Fi connection for example with a tablet or phone or via an internet connection via All Store. The All Store Internet device makes all collected data available online for the user (the owner of the cold store), the contractor (e.g. the French fries factory) and Allround Storage (supplier of the system). Many of the competing systems do not have this capability. The program is extremely user-friendly. The contents of the All Store are very easy to pick up. A very fast connection and log in is a standard part of the storage system. Graphs can easily be generated from the measured values. Here, with common sense, very adequate measures can be taken to correct any disturbances in the storage process. For example, from Co2 you can see whether the door has been open, for example. When the CO2 in a cell goes down, air from outside has entered the cell. A cell with potatoes always has a higher value of CO2 than outside air. The most important values that need to be constantly monitored are listed below. If you have any questions or uncertainties, you can always consult one of our specialists who will then go through the process with you online.
1. Room temperature. What is the temperature in the cell.
2. Product temperature subdivided if desired to all sensors.
3. Channel temperature in bulk storage. This indicates the temperature we press through the potatoes.
4. Evaporator temperature. The evaporator and the temperature gauge of the evaporator are built into the TKC itself. Indicates the value of the heat sink. This can be used to determine whether the chiller is working properly. You can’t set the temperature of the cooling block yourself.
5. Within RH (relative humidity) when it is too high or too low, intervention must be taken. In the case of potatoes, this should be 92%. For onions, 65%. If the RH is too low for potatoes, the humidifier will turn on. With onions when too high, the dryer turns on.
6. Outside RV. ( relative humidity) Depends on conditions and product.
7. CO2 values. It depends on the product.
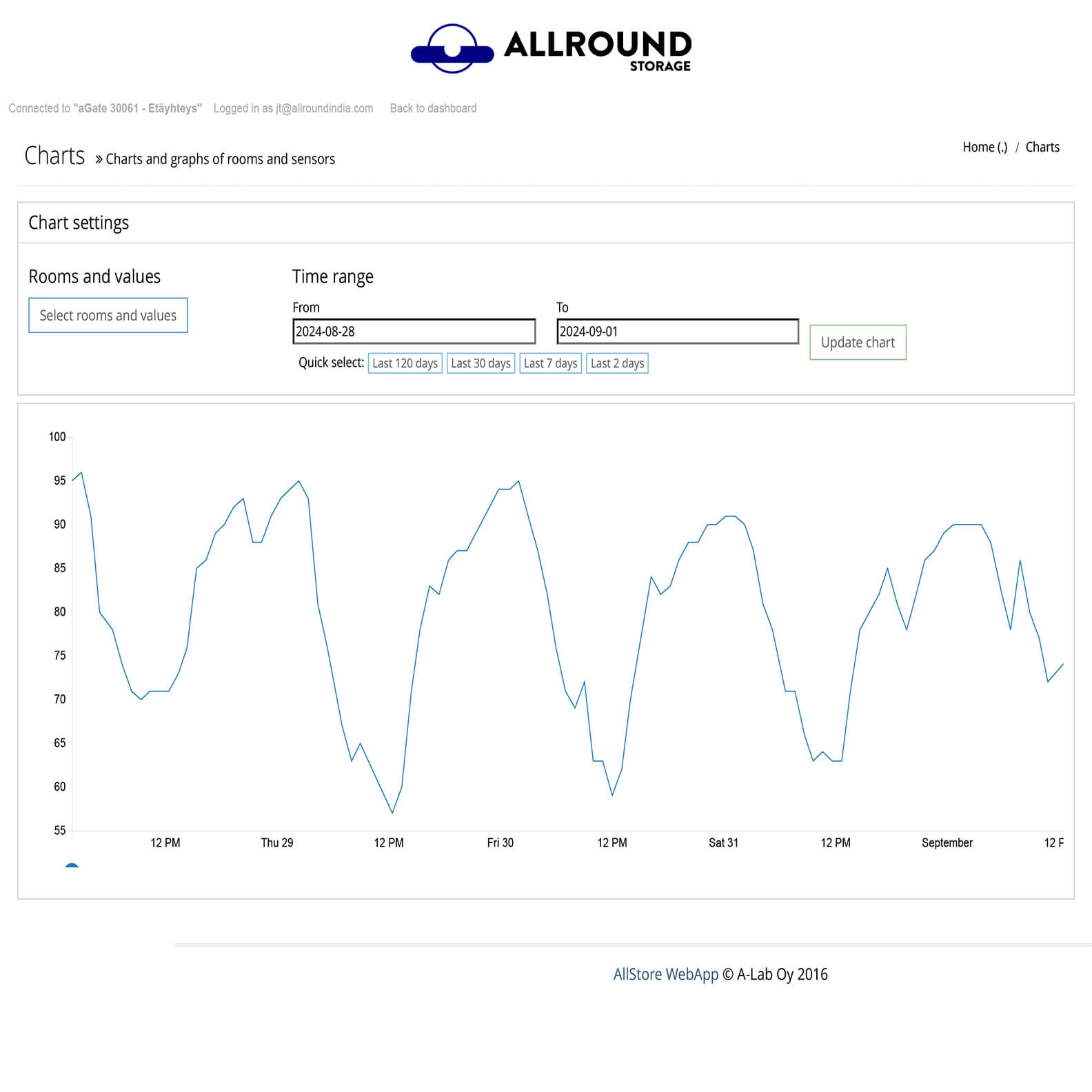
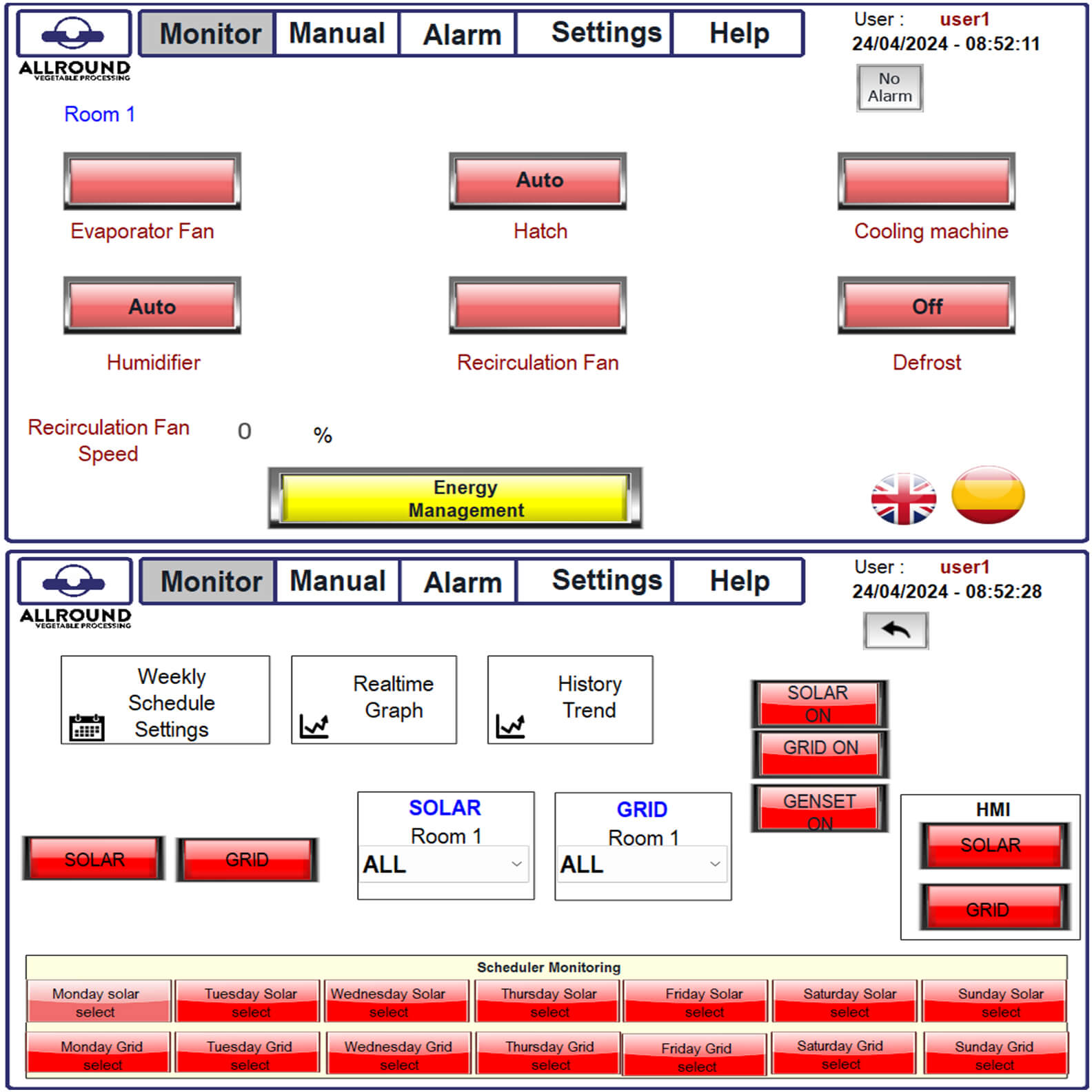
Energy Management
All storage projects will be equipped with an Energy Management program. With the help of this program we can save easily electricity costs. It is easy in storage projects because storage projects are automatic controlled, and in storage we need a limited amount of running hours per day only, and we are free to choose the running hours over the day. Energy Management program Rural: The client has always the choice to bypass the energy management program, with one button you can deactivate the program. We have 3 inputs from the electricity system: Solar, Grid, Generator In case there is solar power available, the input Solar will be activated. In case electricity from grid is available, the input Grid will be activated. In case the generator is started, the input Generator will be activated. For Solar and Grid, the client can choose to run all, it means that mechanical cooling is possible, outside cooling is possible and internal recirculation is possible. Mechanical cooling will consume the biggest part of the energy, so client can also choose to run with outside cooling and recirculation only. For every day of the week you can give individual time slots as well for solar as well for grid. In case we have generator active, all storage activities will be blocked. The idea is that generator will only run a limited hours per day, to be sure that you have electricity for important things as light, water pump, and office. We don’t want to use expensive generator electricity for storage, as long we have enough hours available from solar and grid. “In the energy management system, it is possible to shut down the cooling when peak capacity is required by the entire running line. The storage computer will monitor the circuit values of your cold storage.”
Switch panel
The switch panel is the essential link between the controller and the installed hardware and incorporates all switches and protections for a safe operation of the installation.
The engineers working for Allround storage have already more than 30 years’ experience in developing switch panels in the agricultural storage business.
Before leaving the factory, the panels are thoroughly tested in a situation where a storage situation is simulated, so we know everything is working well.
Standard features
- Main switch
- Motor gearbox hatch control Open-0 -Close-Automatic Switch
- Individual selection Switch Hand-0-Automatic operation
- Failure indication and operation lights
- Thermal overload protections
- The required wiring with 50% overcapacity
- IP 55 sheet steel enclosure
Optional features
- Automatic star/double star starters or frequency controllers
- Electronic capacity controller for the compressor
- Phase and overload protection
- Stainless steel enclosure
As proven in history, in many cases additional equipment will be installed over time. For this reason we calculate from the beginning minimal 30% free space so additional elements can be built in without any problem
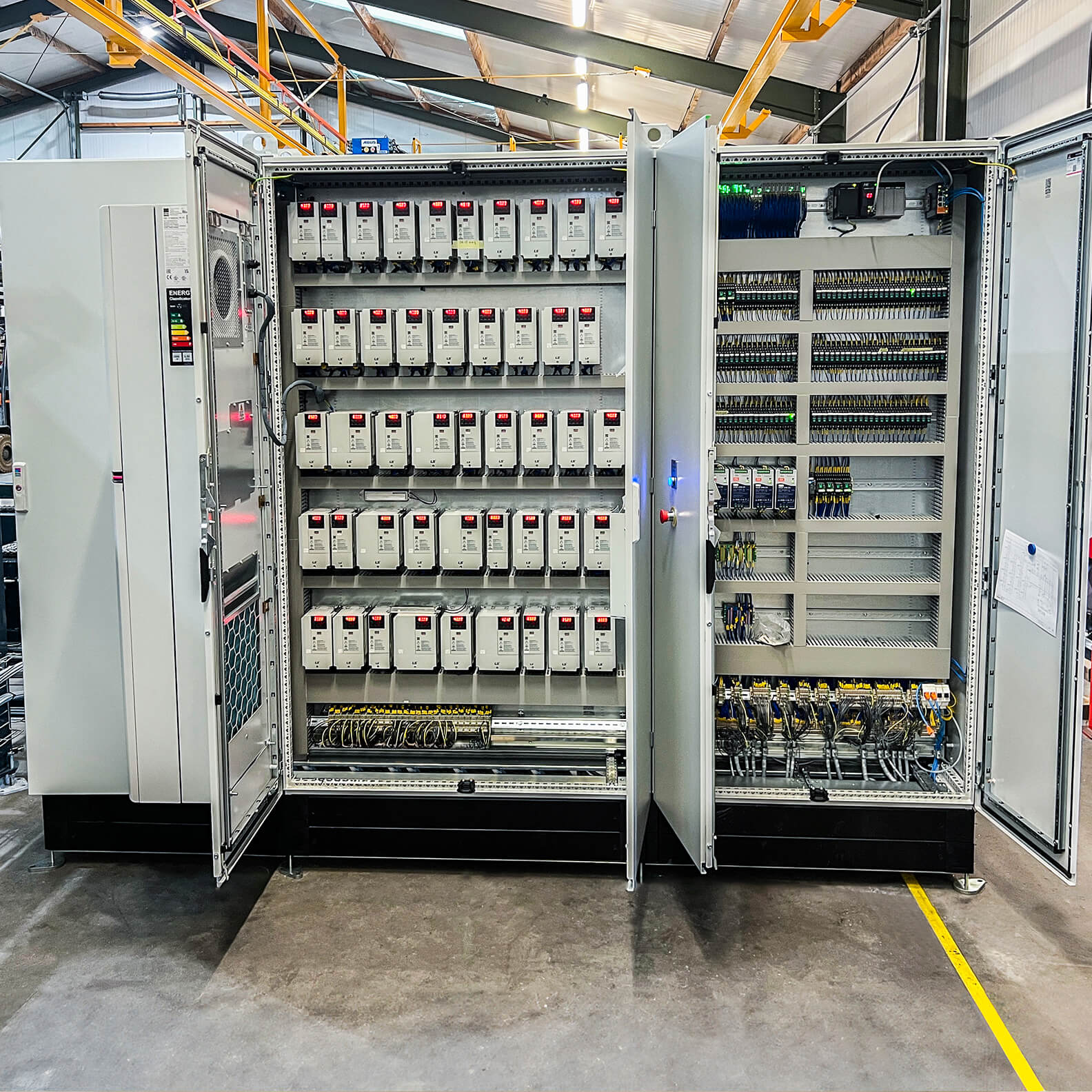